Fresh concrete is that stage of concrete in which concrete can be moulded and it is in plastic state. This is also called “Green Concrete”. Another term used to describe the state of fresh concrete is consistence, which is the ease with which concrete will flow.
Setting of Concrete
The hardening of concrete before its hydration is known as setting of concrete.
OR
The hardening of concrete before it gains strength.
OR
The transition process of changing of concrete from plastic state to hardened state.
Setting of concrete is based or related to the setting of cement paste. Thus cement properties greatly affect the setting time.
Factors affecting setting:
Following are the factors that affect the setting of concrete.
- Water Cement ratio
- Suitable Temperature
- Cement content
- Type of Cement
- Fineness of Cement
- Relative Humidity
- Admixtures
- Type and amount of Aggregate
Workability of Concrete
Workability is often referred to as the ease with which a concrete can be transported, placed and consolidated without excessive bleeding or segregation.
OR
The internal work done required to overcome the frictional forces between concrete ingredients for full compaction.
It is obvious that no single test can evaluate all these factors. In fact, most of these cannot be easily assessed even though some standard tests have been established to evaluate them under specific conditions.
In the case of concrete, consistence is sometimes taken to mean the degree of wetness; within limits, wet concretes are more workable than dry concrete, but concrete of same consistence may vary in workability.
Because the strength of concrete is adversely and significantly affected by the presence of voids in the compacted mass, it is vital to achieve a maximum possible density. This requires sufficient workability for virtually full compaction to be possible using a reasonable amount of work under the given conditions. Presence of voids in concrete reduces the density and greatly reduces the strength: 5% of voids can lower the strength by as much as 30%.
Slump Test can be used to find out the workability of concrete.
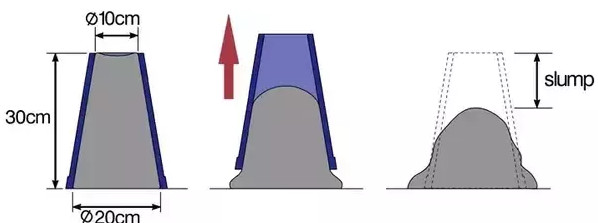
Factors affecting concrete workability:
- Water-Cement ratio
- Amount and type of Aggregate
- Amount and type of Cement
- Weather conditions
- Temperature
- Wind
- Chemical Admixtures
- Sand to Aggregate ratio
Water content or Water Cement Ratio
More the water cement ratio, more will be workability of concrete. Since by simply adding water the inter particle lubrication is increased. High water content results in a higher fluidity and greater workability but reduces the strength of concrete. Because with increasing w/c ratio the strength decreases as more water will result in higher concrete porosity. So, the lower the w/c, the lower is the void volume/solid volume, and the stronger the hardened cement paste.
Increased water content also results in bleeding, hence, increased water content can also mean that cement slurry will escape through the joints of the formwork(Shuttering).
Amount and type of Aggregate
Since larger Aggregate sizes have relatively smaller surface areas (for the cement paste to coat) and since less water means less cement, it is often said that one should use the largest practicable Aggregate size and the stiffest practical mix. Most building elements are constructed with a maximum Aggregate size of 3/4″ to 1″, larger sizes being prohibited by the closeness of the reinforcing bars.
Because concrete is continuously shrinking for years after it is initially placed, it is generally accepted that under thermal loading it will never expand to it’s originally-placed volume. More the amount of aggregate less will be workability.
Using smooth and round aggregate increases the workability. Workability reduces if angular and rough aggregate is used.
Greater size of Aggregate- less water is required to lubricate it, the extra water is available for workability
Angular aggregates increases flakiness or elongation thus reduces workability. Round smooth aggregates require less water and less lubricationand gretaer workability in a given w/c ratio
Porous aggregates require more water compared to non absorbent aggregates for achieving sam degree of workability.
Aggregate Cement ratio
More ratio, less workability. Since less cement mean less water, so the paste is stiff.
Weather Conditions
- Temperature : If temperature is high, evaporation increases, thus workability decreases.
- Wind: If wind is moving with greater velocity, the rate of evaporation also increase reduces the amount of water and ultimately reducing workability.
Admixtures
Chemical admixtures can be used to increase workability.
Use of air entraining agent produces air bubbles which acts as a sort of ball bearing between particles and increases mobility, workability and decreases bleeding, segregation. The use of fine pozzolanic materials also have better lubricating effect and more workability.
Sand to Aggregate ratio
If the amount of sand is more the workability will reduce because sand has more surface area and more contact area causing more resistance. The ingredients of concrete can be proportioned by weight or volume. the goal is to provide the desired strength and workability at minimum expense. A low water-cement ratio is used to achieve a stronger concrete. It would seem therefore that by keeping the cement content high one could use enough for god workability and still have a low w/c ratio. the problem is that cement is the most costly of the basic ingredients. the dilema is easily seen in the graphs below.